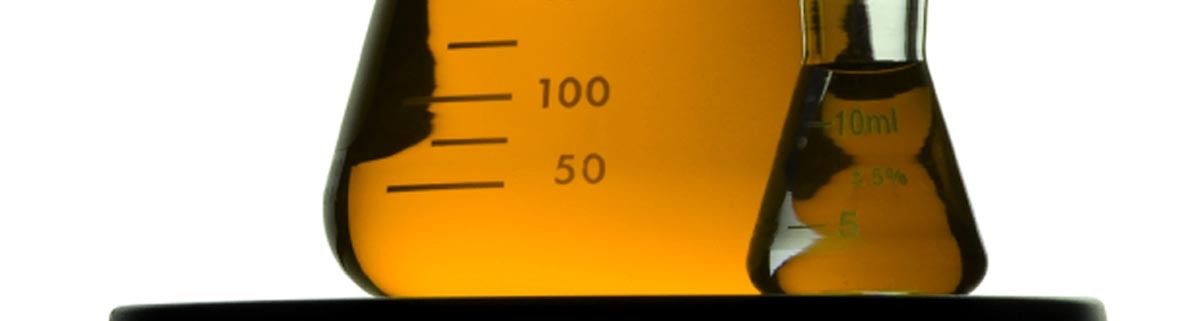
Tertiary-Butyl Polysulfide (TBPS)
TBPS
Di-Tertiary-Butyl Polysulfide (TBPS) is a mercaptan commonly used as a spiking agent for sulfiding hydrotreating catalysts. ChevronPhillips Chemical Company produces TBPS under the trade name “TBPS 454”, while Lubrizol Corporation identifies this chemical with the trade name “SulfrZol® 54”. TBPS offers some benefits over other sulfiding compounds, although several factors should be considered before selecting it as a sulfiding agent.
TBPS differs from DMDS in the following ways:
- Lower decomposition temperature – TBPS decomposes as low as 320°F versus 392°F for DMDS (in the presence of NiMo or CoMo catalysts).
- Lower vapor pressure – TBPS has a lower vapor pressure than DMDS. Polysulfide has an odor similar to sour gasoil.
- Non-flammable – Tertiary-butyl Polysulfide is classified as a non-flammable liquid.
- Decomposition products – The decomposition products of TBPS are H2S, isobutene, and isobutane, while DMDS fully decomposes to H2S and methane. Isobutene and isobutane typically exit the high-pressure separator on the liquid side, improving the purity of the recycle hydrogen and keeping recycle gas density low. Note that the methane make associated with the decomposition of DMDS can be controlled by carefully monitoring H2S levels during the sulfiding process with the use of Reactor Resources’ Online H2S Analyzer and Hydrogen Purity Analyzer.
Other Considerations for Sulfiding with TBPS
Since TBPS contains 54% sulfur as compared to 68% sulfur for Dimethyl Disulfide (DMDS), 25% more product is required to complete the sulfiding of a hydroprocessing unit.
Also note that TBPS can form elemental sulfur when decomposing at intermediate temperature levels if there is not sufficient amounts of hydrogen available. Any sulfur that precipitates out can lead to pressure drop issues in the hydrotreating reactor.
Gas Phase Sulfiding
Extra care must be exercised if polysulfide is utilized for a gas phase sulfiding project. In this case, these guidelines must be followed:
- Inject the TBPS as close as possible to the reactor inlet. Do not inject in front of a furnace or in a long vertical pipe run.
- Avoid exposing the polysulfide to temperatures greater than 300F (150C) before it enters the process stream.
- Ensure sufficient Hydrogen is available to form H2S by using the maximum H2 flow rate during the entire sulfiding procedure. Intermittent stoppage of H2 flow can lead to solid sulfur deposition. Stop TBPS injection immediately if H2 flow is lost.
- The injection point should ensure good dispersion of the TBPS (eg. on top of a pipe). Avoid injecting into a large diameter pipe with a low flow velocity.
- Target an H2S concentration below 1.5 wt% to help manage the sulfiding exotherm. H2S levels above 2% should be avoided for safety reasons.
- Do not start injection until the reactor inlet temperature reaches a range of 400F-420F (205C-220C). Below 400F (205C), decomposition of TBPS in gas phase may be incomplete. Reactor temperatures above 500F (260C) could lead to catalyst damage if sufficient H2S is not present. Do not exceed 500F until H2S breakthrough is confirmed.
Contact Reactor Resources to discuss the optimum sulfiding compound for your application. We are the only sulfiding service company that supplies both Dimethyl Disulfide (DMDS) and Tertiary-Butyl Polysulfide (TBPS). We’ve even had applications where both chemicals used to optimize the sulfiding process and to reduce costs.
SulfrZol® is a registered trademark of Lubrizol Corporation.