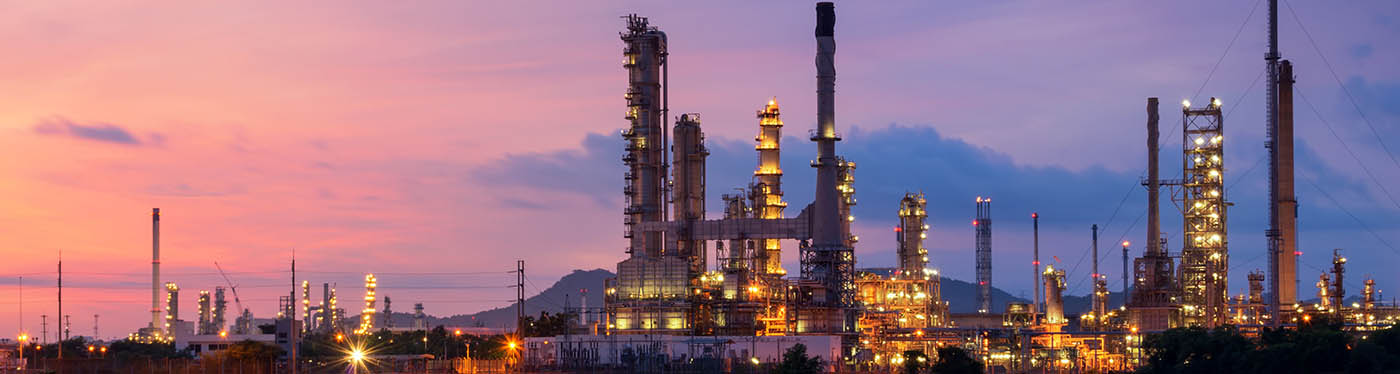
Amine Injection Services
MDEA for Nitrogen Passivation of Cracking Catalysts
Reactor Resources has extensive experience with amine injection services. We typcially inject methyldiethanolamine (MDEA) for passivating hydrocracking catalyst or other chemicals used for in-situ catalyst treatments.
Why Inject Ammonia?
Hydrocracking catalysts tend to be hyper-active in the initial hours following sulfiding. This can lead to catastrophic temperature excursions once reactive feed is introduced to the unit and/or reactor temperatures are raised. Catalyst vendors often recommend ammonia injection following sulfiding in order to temper reactive acidic sites on the catalyst support. Other nitrogen-bearing chemicals, such as tributylamine (TBA), have also been used as an alternative to ammonia. Once they are injected into the reactor at sulfiding conditions, these compounds decompose to form ammonia.
Problems with Ammonia Injection
Issues with Ammonia
Issues with ammonia injection include:
- NH3 has a Health Hazard Rating (HHR) of 3
- NH3 will easily cavitate the injection pump
- Leaks of ammonia can cause a toxic gas cloud
Over-Injection of Nitrogen Compounds
Note that over-injection of nitrogen compounds will result in a catalytic activity that is too low, requiring many days to weeks to desorb the extra nitrogen from the catalyst support. Over-injection also wastes chemicals since ammonia will react with H2S, forming ammonium sulfide salts that can precipitate out downstream from the reactor. In addition, extra DMDS must be injected to make up for the H2S consumed by the ammonia.
Online pH Analyzer System
In order to avoid over-injection in hydrocracking applications, Reactor Resource now provides an online pH Analyzer System to continually measure the pH change of “sour” water exiting the process from the product separator water boot. The pH directly correlates with the nitrogen addition, allowing for more precise control of the nitrogen injection rate. With real-time data from the analyzer, engineers and operations can track the passivation process and be pro-active in fine tuning the nitrogen injection rate.
Amine Injection Services with MDEA as a Passivating Agent
In order to improve the safety and reliability of nitrogen passivation, RxR pioneered the use of MDEA as a passivating agent. Based on its Health Hazard Classification of 1, MDEA is much safer to handle than both TBA and ammonia, while still providing the nitrogen needed for passivation. MDEA has a low cost, a high nitrogen density, and is readily available across North America. In fact, most refiners are already using this chemical in their sulfur plant to treat sour gas.
Online pH Analyzer
Optimization of the nitrogen injection can be achieved by closely monitoring the pH change of water from the separator boot. Accurate measurement of the pH can be difficult to achieve, however, since the evolution of NH3 is rapid once the catalyst bed becomes saturated with nitrogen. In order to measure pH quickly and accurately, Reactor Resources, offers an Online pH Analyzer System that connects to your process. Real-time pH measurement prevents over-injection of nitrogen compounds, which can negatively effect product yields and taking days, if not weeks, to recover from.
Improving Renewable Fuel Yields with Nitrogen
Refiners can realize substantial margin gains by improving yields on hydrocrackers and renewable diesel units. These units typically use moderate to highly acidic catalysts to crack larger molecules into shorter more desirable hydrocarbon chains. Reactor Resources has developed a new technique to optimize yields in these units by controlled addition of nitrogen compounds after sulfiding. The nitrogen compounds are adsorbed on the catalyst surface, gently passivating the acidity of the zeolitic supports. This effectively tempers hyperactive catalytic sites, providing improved product yields by reducing over-cracking that can result in increased production of LPG and low-octane naphtha.
Contact Us to discuss how our systems can minimize the risks of exotherms and improve product yields.